​Laser Cleaning Technology:
The Future of Precision Surface Treatment
Why Laser Cleaning?
Laser cleaning, compared with traditional methodologies, presents numerous impressive benefits. Armour Coatings is at the forefront of this transformation, ensuring that we step into the future of cleaning technology with confidence and efficiency.
Not only can we clean steel and other metallic substrates, we can also clean many different substrates inlcuding, brick, stone, concrete, timber and more.
Laser cleaning offers little or no mess solution over conventional grit blasting, hydro-blasting or simple grinding of the surface.
Generally, the underlaying surfaces cleaned with lasers are not damaged and are cleaned, ready to use or to be recoated.
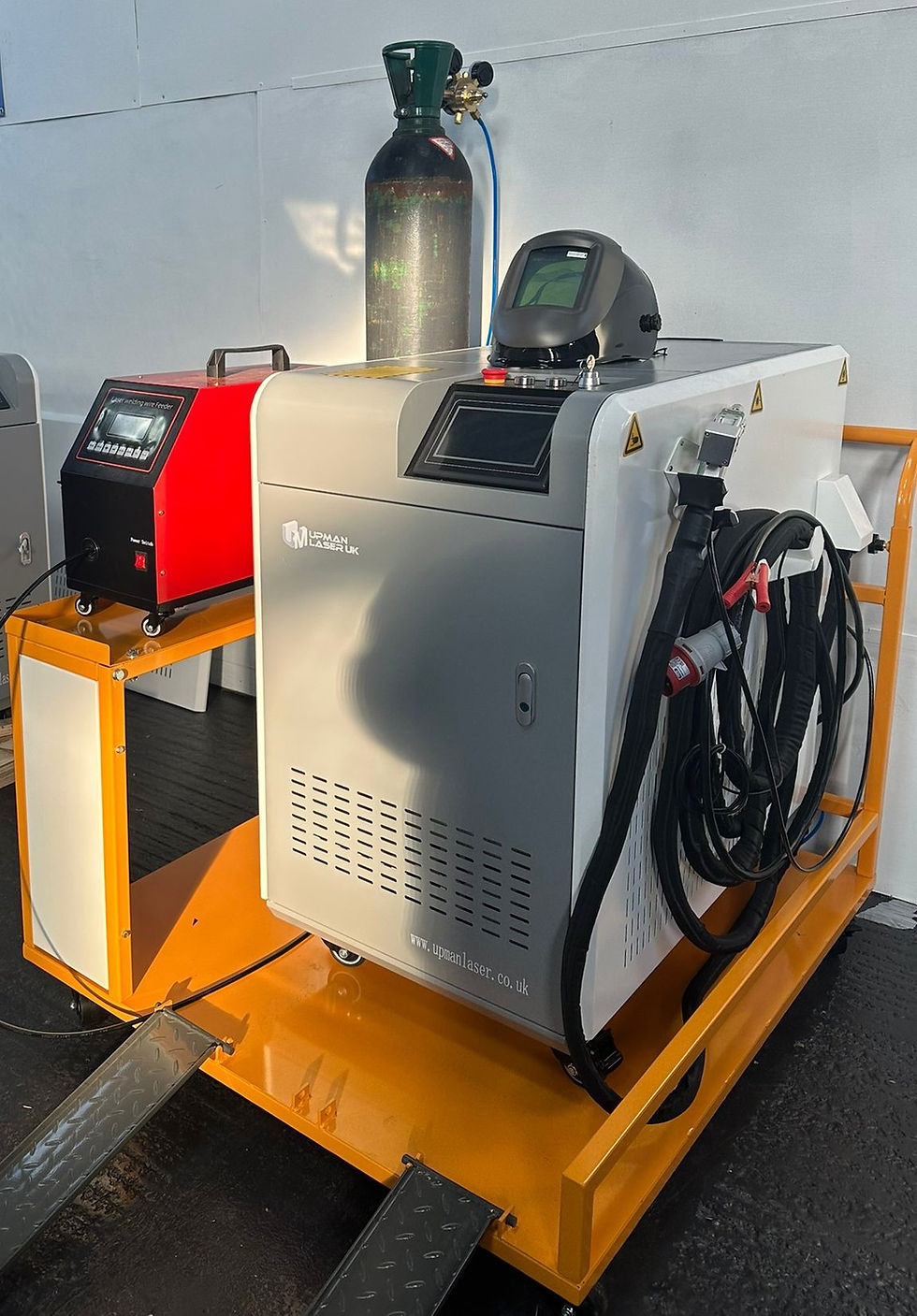

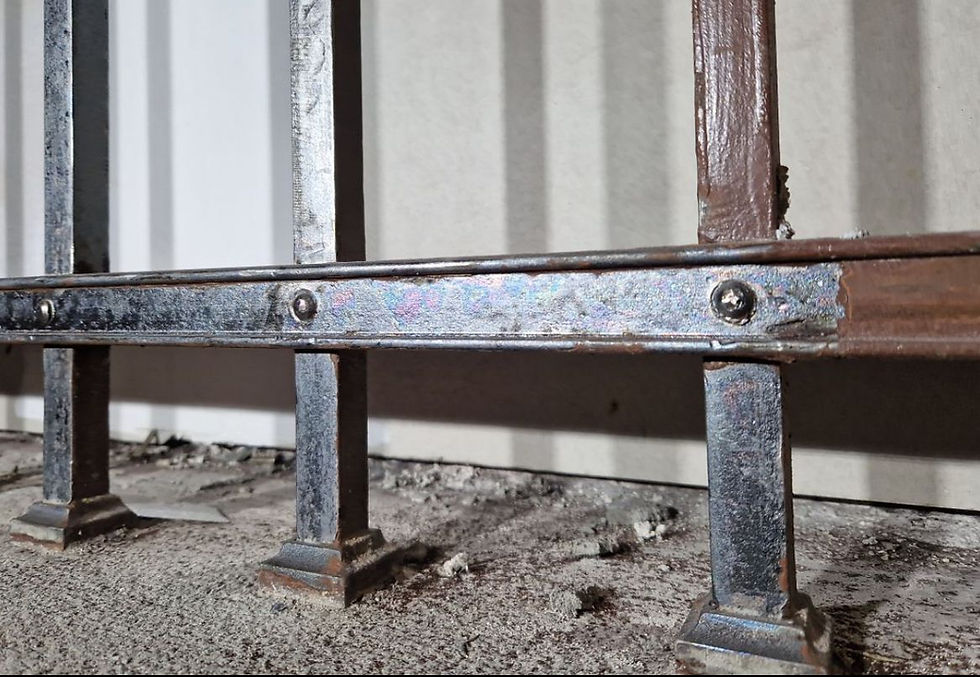
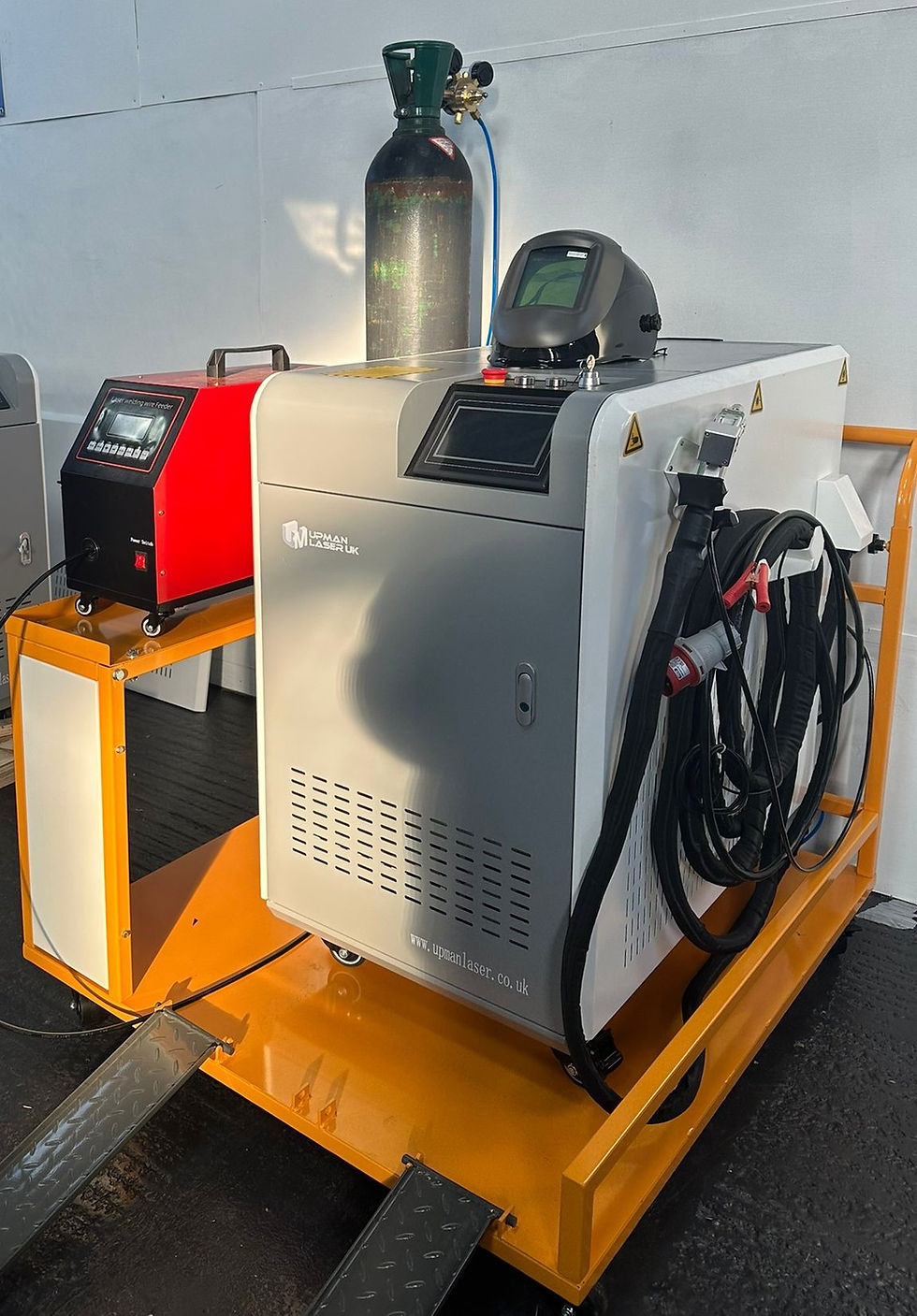
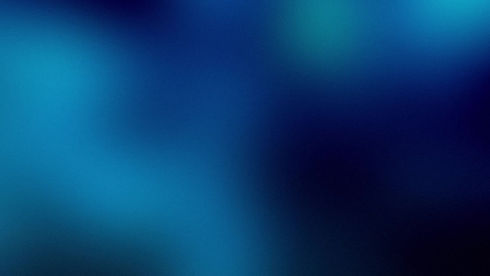
Comparative Analysis:
CW Lasers vs. Pulse Lasers
CW Lasers:
Power Limitations: No units are available below 1000W.
Operational Mechanism: “CW” denotes Continuous Wave. This means when activated, the laser beam continually interacts with the surface. Contaminants are dislodged due to the constant energy transfer, which heats and excites the particles, causing detachment from the substrate.
Heat Transfer: Notably higher heat transfer is involved, often necessitating hot work permits and extended cool-down durations.
Applications: Best suited for removing heavy rust and thick paint layers.
Pulse Lasers:
Power Range: Units are commonly available from 500W to 2000W.
Operational Mechanism: The laser beam pulsates, making intermittent contact with the surface approximately every nanosecond. While there‘s still some heat transfer beneficial for contaminant removal, it’s significantly milder, ensuring the substrate remains well-protected.
Applications: Primarily utilised for cleaning lighter rust, oils, resins, paints, and more delicate surfaces.
​
Gaussian Beams: These have narrowly focused, intense individual pulses. While they‘re effective for heavier removal tasks, there‘s a heightened chance of surface etching. They offer a suitable alternative to CW lasers, especially when excessive heat transfer poses challenges.
Flat-Top Beams: Enables operators to achieve high precision in terms of the metal’s finish. Ideal for tasks like industrial mold cleaning, where a mirror finish is paramount, or in scenarios demanding a gentler approach.
-
Eco-Friendly and Safe
Unlike conventional methods, laser cleaning completely eliminates the need for solvents and abrasives. This not only benefits the environment but also ensures a safer workspace as there are no abrasive materials to handle or dispose of.
​
-
Precision and Control
Where traditional processes can often be generic and manually intensive, laser cleaning offers precision.
It can be meticulously controlled to target specific areas on a component, ensuring that only the desired sections are cleaned without affecting the rest.
​​
-
Repeatability and Consistency
In an era where stringent quality standards are becoming the norm, laser cleaning stands out.
It guarantees consistent repeatability, meeting and often surpassing the rigorous benchmarks set by quality assurance protocols.
-
Efficiency & Simplicity​
With just a simple power-up, laser cleaning enables cleaning without the need for chemicals, media, or water. Its adjustable focus allows for precision cleaning, ensuring every surface detail is addressed with any substrate damage. Lasers can reduce the amount of time spent cleaning in many situations, as they are an efficient and precise tool.
​​
-
Versatility
Effortlessly remove contaminants like resin, paint, oil, stains, dirt, rust, coatings, plating, graffiti and oxide layers. Our process is versatile, catering to a wide array of industries including nuclear, chemical, ship building, auto repair, construction, food industry, railways, and anywhere where a fast, clean and versatile cleaning system is required.
​
-
Understanding Laser Cleaning Technology
Laser cleaning harnesses high-energy laser beams directed at the workpiece surface. This causes impurities, rust, or coatings to evaporate or peel off instantaneously. The process is non-abrasive, ensuring that your valuable materials remain unharmed during cleaning. The result is an effective and rapid removal of unwanted adhesions or coatings, realising a pristine cleaning process. This innovation is rooted in the intricate interaction between laser and matter.
​
Laser Cleaning Equipment: The Future of Precision
Surface Treatment
A state-of-the-art solution in surface
treatment technology.